Samba Step system expands composites research for Augsburg University
Germany-based university intends to use Cevotec’s FPP-based Samba Step system for field research of ceramic fiber composites.
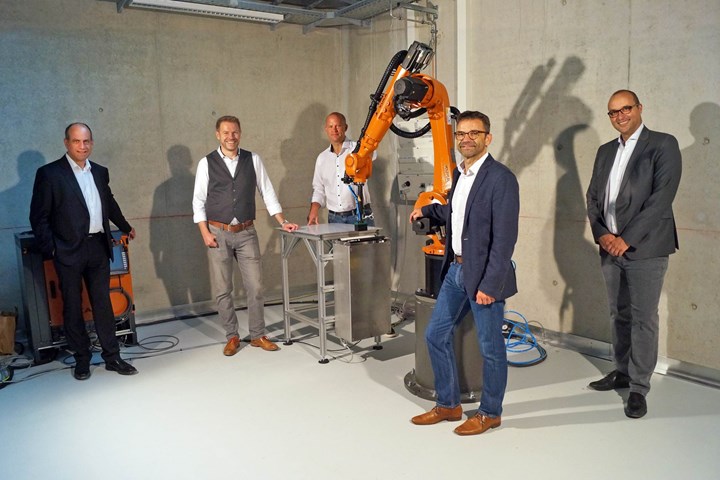
Cevotec’s SAMBA Pro System at MRM Augsburg. From left to right: Dr. André Baeten (Augsburg University of Applied Sciences), Thorsten Gröne (Cevotec), Arne Muncke (Cevotec), Dr. Dietmar Koch (Augsburg University), Dr. Neven Majić (Augsburg University of Applied Sciences) Photo Credit: Cevotec, Augsburg University
Two research organizations have joined forces for projects on patch-based fiber layup: The Institute of Materials Resource Management (MRM) at (Augsburg, Germany), which focuses on ceramic fiber composites and data-driven computational materials science, and the faculty of mechanical engineering at (Augsburg, Germany).
Augsburg University intends to use Cevotec’s (Munich, Germany) Samba Step system for field research of ceramic fiber composites. The system is based on fiber patch placement (FPP) technology. “Samba Step systems, with their flexible degree of automation, are explicitly designed for prototyping and product development in R&D departments, institutes and universities,” explains Thorsten Groene, CEO of Cevotec. Prof. Dietmar Koch, head of materials engineering at MRM, adds, “We will investigate the patch-based process using ceramic fiber composites for new applications.”
With the installation of a Samba Step system at MRM in Augsburg, Cevotec also continues the existing cooperation with Augsburg University of Applied Sciences. Prof. Neven Majić, one of Cevotec’s co-founders now dedicated to developing FPP technology at the Augsburg institute, comments, “AI is a relevant research topic for us. Fiber patch placement represents an innovative composite production technology with increased degrees of freedom. This offers a huge potential for AI development in patch-based composites manufacturing.”
While the Augsburg University was responsible for setting-up the initial Samba Step system, the Augsburg University of Applied Sciences will take over the future expansion with a sensor-intensive automated feeding unit. The Samba system, all parties agree, forms a solid foundation for joint research projects to come.
Related Content
-
ADTC to celebrate grand opening for hands-on composites training
The training center’s launch, to include facility tours, demonstrations and networking opportunities, coincides with CAMX in Orlando.
-
AMRC Training Centre introduces composites apprenticeship opportunity
With partners McLaren and Teledyne CML Composites, the Training Center will train new composites technicians in South Yorkshire to build up the future industry workforce.
-
New online training course targets prepreg basics
JEC World 2024: Composites Expert highlights how its E-Learning Composites Academy platform supports flexible industry learning with new courses developed with Stelia Aerospace North America.