NTU Singapore, Arkema manufacture carbon fiber helmets using Elium resin
Carbon fiber reinforcement increases stiffness, toughness of the helmet’s outer shell and allows it to absorb more impact energy over a longer period.
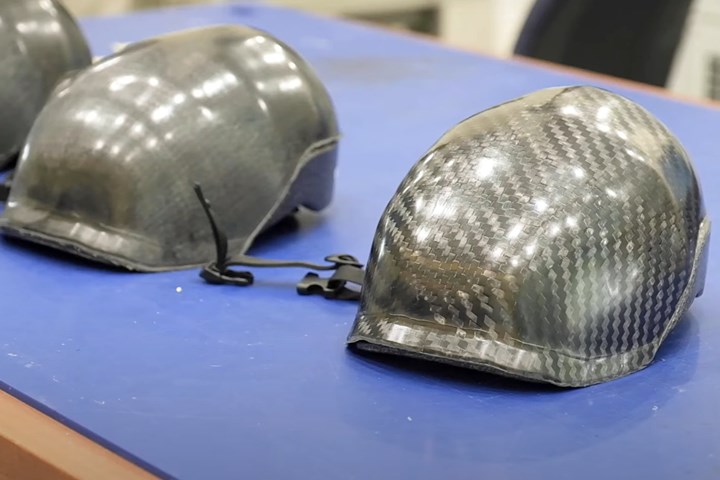
Photo Credit: NTU Singapore
A team of researchers from Nanyang Technological University’s (NTU) School of Mechanical and Aerospace Engineering (Singapore), in collaboration with French specialty materials company Arkema (Colombes, France), have developed a safer bicycle helmet using a combination of composite materials, which the company says offer the same protection of current top-tier helmets, but potentially at the price of mid-tier helmets.
The helmets’ outer shell is made from Arkema’s Elium liquid thermoplastic resin (see “Arkema wins Pierre Potier Prize for Elium thermoplastic resin”) and is reinforced with carbon fiber. The helmets were also manufactured via a molding process the NTU team developed with Arkema engineers for Elium. Overall, the carbon fiber reinforcement reportedly makes the outer shell tougher, stiffer and less brittle than a polycarbonate shell. It also increases the helmet’s contact time, which is the total time of impact in which the helmet experiences impact load.
Together, says the partners, these properties allow the outer shell to absorb more impact energy over a longer period, while also dissipating it evenly throughout the helmet. This results in less overall force reaching the head, thereby reducing the chances of critical injury.
To test the helmets, the team sent them hurtling at high speeds down at metal anvils with enough force to crack open a durian. According to results, the helmet’s composite outer shell was able to absorb the bulk of the impact, providing better results than current mass-produced helmets.
Related Content
-
CirculinQ: Glass fiber, recycled plastic turn paving into climate solutions
Durable, modular paving system from recycled composite filters, collects, infiltrates stormwater to reduce flooding and recharge local aquifers.
-
Low-cost, efficient CFRP anisogrid lattice structures
CIRA uses patented parallel winding, dry fiber, silicone tooling and resin infusion to cut labor for lightweight, heavily loaded space applications.
-
Plant tour: Teijin Carbon America Inc., Greenwood, S.C., U.S.
In 2018, Teijin broke ground on a facility that is reportedly the largest capacity carbon fiber line currently in existence. The line has been fully functional for nearly two years and has plenty of room for expansion.