NCC digital design trial speeds up composite pressure vessel proof of concept
Application of multi-disciplinary optimization (MDO) techniques determines optimal composite hydrogen pressure vessel design five times faster, says the NCC.
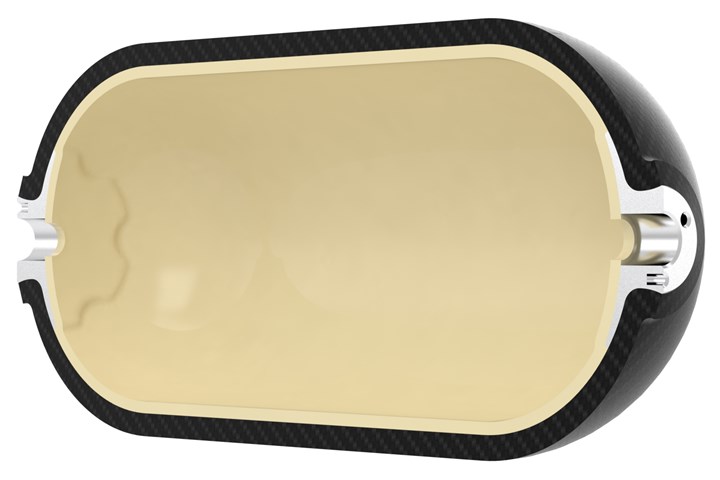
DETI hydrogen pressure vessel rendering. Photo Credit: National Composites Centre (NCC).
The (NCC, Bristol, U.K.) has successfully completed a proof-of-concept project that demonstrates the transformative impact of digital tools on the design process for the complex engineering industry.
The application of multi-disciplinary optimization (MDO) techniques to a composite hydrogen pressure vessel has resulted in identifying an optimum design that is said to be five times faster than a traditional, sequential approach, in addition to reducing the risk of human error in the process of data transfer. Offering a new approach to redesigning and remaking sustainable products, the NCC says it enables increased agility and opportunities to innovate faster, driving competitive advantage and engineering leadership.
“We have demonstrated the potential efficiencies in product, process and productivity that can be achieved to accelerate digital engineering transformation,” Marc Funnell, director of digital engineering at the NCC, says. “Through DETI and Digital Engineering at the NCC, our proof of concepts and test beds help manufacturers to innovate, develop and de-risk rapidly configurable projects and industrial digital technologies before investment.”
Undertaken as part of , a strategic program of the (WECA), the project demonstrates the opportunity to address all design elements of a product at the same time, resulting in optimized design, lower development costs, faster new product introduction and the ability to refine specific features to meet contrasting demands of different applications.
HEEDS MDO, a design space exploration and optimization software from the Simcenter portfolio by Siemens Digital Industries Software (Plano, Texas, U.S.) was the platform selected for the implementation of the MDO process. Fifty designs were evaluated in less than two hours and an optimal solution was discovered among twenty-three feasible designs that satisfied all the constraint requirements.
The NCC says the proof of concept can be easily applied to other products and sectors, adapting the automated design process to quickly explore and optimize designs that address different objectives under a different set of constraints.
The NCC is part of a multi-partner collaboration called the , which brings together the strengths and capabilities of the Network and partner innovation centers to accelerate innovation, develop growth in the U.K. hydrogen supply chain and overcome technology and integration challenges to establish an effective U.K. hydrogen economy. This project in particular highlights the NCC’s credibility and expertise, delivering R&D and technology pull through from fundamental research to industrial application across four strategic areas: advanced composites, digital engineering, hydrogen and sustainability, to address complex global challenges.
More detailed information about the application of MDO to the hydrogen pressure vessel can be viewed in this .
Related Content
-
Composites end markets: Energy (2024)
Composites are used widely in oil/gas, wind and other renewable energy applications. Despite market challenges, growth potential and innovation for composites continue.
-
RTM, dry braided fabric enable faster, cost-effective manufacture for hydrokinetic turbine components
Switching from prepreg to RTM led to significant time and cost savings for the manufacture of fiberglass struts and complex carbon fiber composite foils that power ORPC’s RivGen systems.
-
We4Ce infused 2.5-3-MW rotor blade design passes validation test
Composite rotor blade structure design by We4Ce, mold and prototype production by InDutch Composites and fatigue testing by Suzlon Group has resulted in the novel blade’s IEC61400-5:2020 certification.