EUVAM project investigates energy-efficient UV process for composites curing
University of Stuttgart researchers intend to develop flexible, highly productive and digitally controllable manufacturing approach for small urban vehicle production.
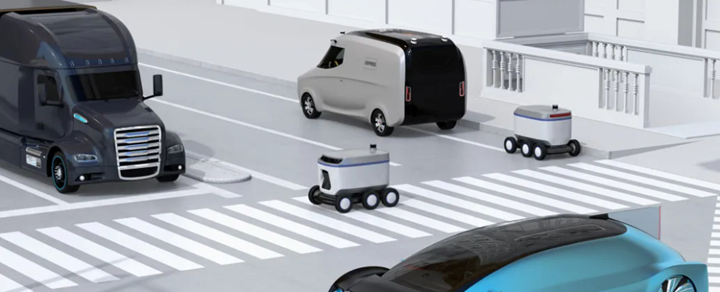
The EUVAM project is focusing on lightweight components for the structure of small urban vehicles. Photo Credit: Depositphotos
EUVAM, a new research project at the University of Stuttgart’s (Germany) will investigate curing fiber-reinforced polymers (FRP) using ultraviolet radiation (UV) to further optimize cycle times and energy consumption associated with the production of lightweight structural composite components.
The focus of the EUVAM project is to develop an energy- and time-efficient manufacturing process in order to meet the high demands of the mobility industry in terms of lightweight construction, economy and sustainability. The aim is, among other things, to implement the integration of non-transparent carbon fibers in UV-cured FRP through optimized process control in order to enable structural assemblies in the context of urban micro vehicles.
Compared to traditional FRP curing processes, the university researchers believe significant costs can be saved with the help of energy-efficient UV process control. UV curing would make isothermal process control for polymer curing in resin transfer molding (RTM) or in the wet pressing process obsolete, thus reducing time to completion, all without sacrificing final mechanical properties.
Specifically, through the use of photo-initiated polymers in the context of high-performance, fiber-reinforced lightweight construction methods, a flexible, highly productive and digitally controllable manufacturing approach can be implemented.
A demonstration of the developed technologies and concepts concludes with the implementation of a demonstrator, which is to be integrated into the ICM demonstrator vehicle (BUP14).
This project is funded by the Ministry of Science, Research and Art.
Related Content
-
Carbon fiber composite pallet revolutionizes freight industry
LOG Point Pallet fuses advanced materials with innovative design and manufacturing to improve supply chains worldwide.
-
Plant tour: Aernnova Composites, Toledo and Illescas, Spain
RTM and ATL/AFP high-rate production sites feature this composites and engineering leader’s continued push for excellence and innovation for future airframes.
-
The potential for thermoplastic composite nacelles
Collins Aerospace draws on global team, decades of experience to demonstrate large, curved AFP and welded structures for the next generation of aircraft.