Composites for structural batteries
Researchers in Sweden find carbon fiber composites can be used for creating structural batteries that could help minimize mass in EVs and consumer electronics.
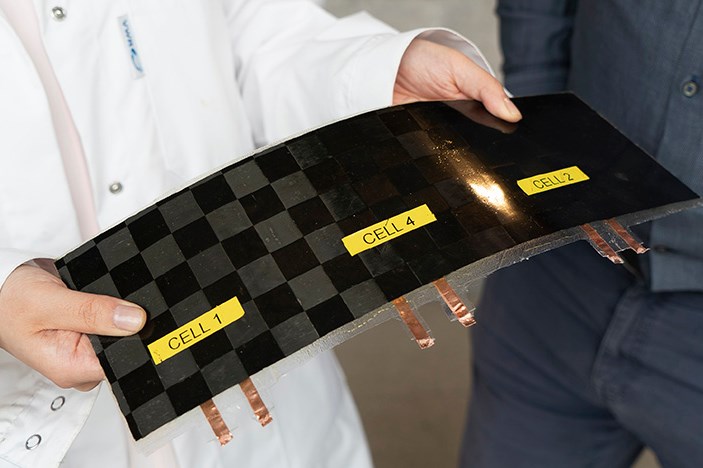
Fig. 1. A multicell laminate manufactured in Chalmers’ composite lab provides not only energy density but structural properties. Photo Credit: Chalmers Institute of Technology
One of the issues faced by engineers developing electric vehicles (EVs) is the mass of the batteries necessary to provide power to the motors. The batteries are heavy. This means that in order to get range—one of most required features for an EV—there needs to be sufficient battery capacity… but this becomes something of a vicious cycle as more battery means more mass and more mass means reduced range.
Researchers at in Sweden have developed a battery that could be a solution to this problem as it not only stores energy (24 watt-hours per kilogram), but it provides structural support, as it has a stiffness of 25 GPa.
Leif Asp, professor at Chalmers and leader of the research project, which is being run in collaboration with the KTH Royal Institute of Technology (Stockholm, Sweden), said, “Previous attempts to make structural batteries have resulted in cells with either good mechanical properties, or good electrical properties. But here, using carbon fiber, we have succeeded in designing a structural battery with both competitive energy storage capacity and rigidity.”
In a paper in (vol. 2, issue 3), Asp and his coauthors describe the battery:
“The structural battery composite consists of a CF [carbon fiber] negative electrode and an aluminum film‐supported positive electrode separated by a GF [glass fiber] separator in a SBE [structural battery electrolyte] matrix material. Consequently, the CFs act as host for Li (i.e., active electrode material), conduct electrons and reinforce the material. Similarly, the positive electrode foil provides combined mechanical and electrical functionality. The SBE facilitates Li‐ion transport and transfers mechanical loads between fibers, particles and plies. Two types of GF fabric separators, a Whatman GF/A and a GF plain weave, are used as model materials to investigate the effects of separator thickness and architecture, as well as material anisotropy, on the multifunctional performance.”
At present they are working on a new structural battery with the aluminum film being replaced by carbon fiber and the use of a thinner fiberglass separator.
Asp said that he expects that further research will result in a battery that has an energy density of 75 watt-hours per kilogram and a stiffness of 75 GPa.
“If you look at consumer technology,” Asp said, “it could be quite possible within a few years to manufacture smartphones, laptops or electric bicycles that weigh half as much as today and are much more compact.”
Related Content
-
Thermoplastic composites: Cracking the horizontal body panel nut
Versatile sandwich panel technology solves decades-long exterior automotive challenge.
-
ASCEND program completion: Transforming the U.K.'s high-rate composites manufacturing capability
GKN Aerospace, McLaren Automotive and U.K. partners chart the final chapter of the 4-year, £39.6 million ASCEND program, which accomplished significant progress in high-rate production, Industry 4.0 and sustainable composites manufacturing.
-
Braided thermoplastic composite H2 tanks with co-consolidated molded boss areas to fit EV battery space
BRYSON project demonstrates possible designs, automated manufacturing and low permeability concepts, including EVOH liner and novel PPA matrix.