AZL Aachen webinar: Designing with thermoplastic composites
AZL Aachen is hosting the fifth webinar in its Lightweight TechTalk series, titled, “Best Practices in Lightweight Design with Thermoplastic Composites” on Thursday, Jan. 28, 1:00-2:45 p.m. (13:00-14:45) CET.
AZL Aachen TechTalk #5 agenda. Photo Credit: AZL Aachen
Service and engineering provider for lightweight technology and business development AZL Aachen (Aachen, Germany) is hosting the fifth webinar in its Lightweight TechTalk series, titled, “” on Thursday, Jan. 28, 13:00 pm-14:45 pm CET.
In this upcoming Lightweight TechTalk design and simulation experts will share their experiences and insights on lightweight design enabling design for profitability. A “Meet the Speaker” session following the talk (from 15:00-16:00 pm CET) will allow participants to book 5-minute slots with the speakers to match interest and exchange.
With the series of compact "Lightweight TechTalks" AZL is providing a digital platform for networking and presenting technology and market insights to the international lightweight community.
Speakers include:
- Sebastiaan Haanappel, Aniform
- Maiko Ersch, Institute for Plastics Processing (IKV) in Industry and Craft at RWTH Aachen University
- Ferrie van Hattum, ThermoPlastic Composites Application Center
- Warden Schijve, AZL
To encourage networking among attendees, a participant profile is available for attendees to report their interests, contact details and LinkedIn profile, to be shared this information with the other attendees.
Attendance of AZL Aachen’s Lightweight TechTalk series is free. Click for more information and to register.
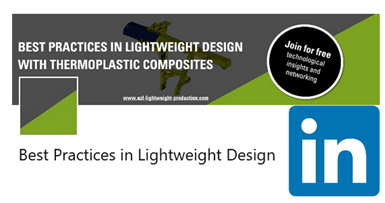
In addition to the Lightweight TechTalk, AZL has opened a on the talk topic to allow for networking and knowledge exchange beyond the TechTalk. Content of previous Lightweight TechTalks can be downloaded .
Related Content
-
Aurora reveals latest SPRINT X-Plane design concept
An Aurora and Boeing team advances its high-speed, vertical lift concept to the preliminary design phase, which features three lift fans, a more refined composite exterior and an uncrewed cockpit.
-
Testing to support composite bolted joint analysis
An overview of ASTM Standard Guide D8509, and its coupon-level mechanical testing of design properties for analyzing composite bolted joints.
-
Proving thermoplastic composites match carbon fiber/epoxy performance in road bikes
CDCQ, LxSim, Addcomp and Argon 18 collaborate to optimize a carbon fiber/PA6 bike seat post, democratizing AFP and demonstrating materials and process for future designs and production.