Airbus begins assembly of first Wing of Tomorrow prototype
The program brings together more than 100 new technologies and composites innovations, including delivery of the first fixed trailing edge by GKN Aerospace.
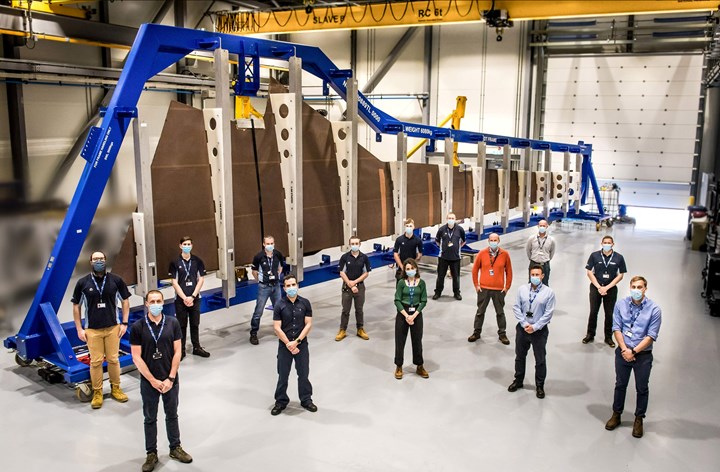
Airbus’ (Toulouse, France) Wing of Tomorrow (WoT) program has reached a new milestone with the assembly of the program’s first full-size wing prototype, the company announced on Sept. 22.
In total, three full-size prototype wings will be manufactured. The first will be used to understand systems integration, the second will be structurally tested to compare against computer models, and the third will be assembled to test scaling up production and to compare against industrial modeling.
WoT, funded in part by the U.K.’s Aerospace Technology Institute, is a fully transnational Airbus program involving global partners and teams across Airbus’ European sites, including Bremen in Germany, where the Wing Moveables team is based. The three wing demonstrators will bring together more than 100 new technologies to explore new manufacturing and assembly techniques with the goal of making aviation more sustainable, Airbus says.
Sabine Klauke, Airbus CTO, says, “High-performing wing technology is one of several solutions — alongside sustainable aviation fuels and hydrogen — we can implement to contribute to aviation’s decarbonization ambition. Wing of Tomorrow is also an example of how large-scale industry collaboration will be critical to achieving our sector’s agenda for a more sustainable future.”
Sub-assembly of the complex wing cover took place at Airbus’ Filton, U.K. site, having been manufactured at the National Composite Centre in Bristol.
GKN Aerospace delivers fixed trail leading edge
Also announced on Sept. 22 by GKN Aerospace (Redditch, U.K.), the company has delivered the program’s first fixed trailing edge (FTE) from GKN Aerospace’s global technology center in Bristol, employing large-scale resin transfer molding (RTM) and building on the completion of a single-piece wing spar earlier this year.
GKN Aerospace says the technology deployed sees a move away from traditional, pre-impregnated resin material to dry composite fibers that are injected with resin as part of the initial manufacturing process. This is said to result in significant weight savings, removes one third of the production steps and significantly reduces energy consumption.
Advances in the automation of assembly of the FTE are reported to demonstrate significant benefits in quality, repeatability and assembly time necessary to meet the requirements of high-rate wing manufacture.
According to Airbus, the wing cover and the fixed trailing edge were delivered to the Advanced Manufacturing Research Centre (AMRC) in Wales and assembled at Airbus’ wing production plant in Broughton, U.K.
Chris Everett, GKN Aerospace senior VP – Airbus Business, says, “The delivery of the first Wing of Tomorrow program trailing edge into Airbus marks a significant step forward in the technology deployment for this type of application. Advances in composite manufacture and automated assembly techniques are set to demonstrate the ability to both produce such items at high rate while delivering significant reductions in energy utilization and waste.”
John Pritchard, president civil airframe of GKN Aerospace, says, “The manufacturing of the first composite fixed trailing edge under the Wing of Tomorrow program is a great achievement. We are proud to be on board of Airbus’ Wing of Tomorrow research program. The manufacturing of lighter, stronger and low maintenance composite wing structures will contribute to the sustainability goals of the aerospace industry and help shape the future of flight.”
Additional WoT advancements covered by ÂÌñÏ×ÆÞ include a rear spar and thermoplastic ribs developed by Daher (Paris, France), thermoplastic ribs developed by GKN Aerospace and a lower wing skin developed by Spirit AeroSystems (Wichita, Kan., U.S.).
According to Airbus, WoT aims to not only test the latest composite materials and new technologies in aerodynamics and wing architecture, but to also explore how wing manufacturing and industrialization can be improved to meet future demands as the sector emerges from the pandemic.
Related Content
Plant tour: Aernnova Composites, Toledo and Illescas, Spain
RTM and ATL/AFP high-rate production sites feature this composites and engineering leader’s continued push for excellence and innovation for future airframes.
Read MoreThe next-generation single-aisle: Implications for the composites industry
While the world continues to wait for new single-aisle program announcements from Airbus and Boeing, it’s clear composites will play a role in their fabrication. But in what ways, and what capacity?
Read MoreInfinite Composites: Type V tanks for space, hydrogen, automotive and more
After a decade of proving its linerless, weight-saving composite tanks with NASA and more than 30 aerospace companies, this CryoSphere pioneer is scaling for growth in commercial space and sustainable transportation on Earth.
Read MoreFirst Airbus A350 crash confirmed in Haneda
Shortly after touch-down, a JAL A350-900 aircraft recently collided with a De Havilland Canada Dash 8. Exact circumstances are still unknown.
Read MoreRead Next
Update: Lower wing skin, Wing of Tomorrow
Airbus is evaluating several advanced composites technologies as part of its Wing of Tomorrow program. Among these is liquid resin infusion of the lower wing skin, being developed by Spirit AeroSystems.
Read MoreWing of Tomorrow ribs: One-shot, thermoplastic, OOA consolidation
GKN Aerospace’s carbon fiber thermoplastic aircraft rib design accomplishes 45-minute cycle times, reduced weight and competitive costs via a customized press system.
Read MoreOut-of-autoclave VBO rear spar, thermoplastic ribs target Wing of Tomorrow
French Tier 1 aerospace supplier Daher develops out-of-autoclave materials and process technologies for application in next-gen structures for the Airbus Wing of Tomorrow program.
Read More