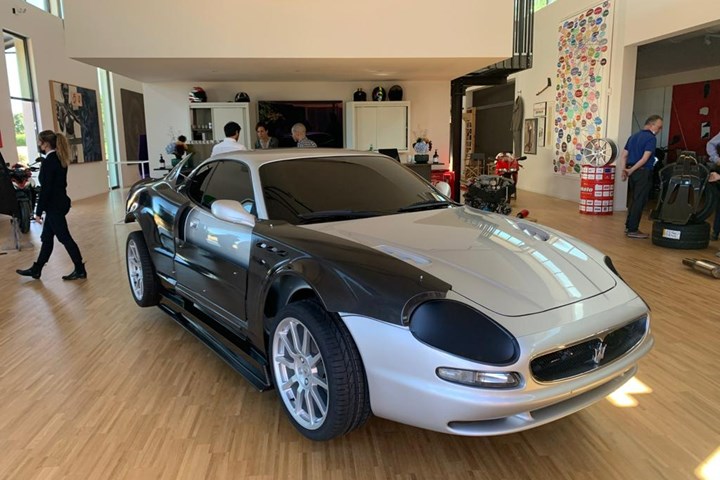
The partially completed Restomod Maserati MV 3200 GTC on display in July 2021. Using custom 3D-printed composite molds, Bercella is delivering 26 total carbon fiber composite body components for installation on the restored vehicle. Photo credit, all images: Bercella S.r.l.
In June 2021, multi-axis machining specialist CMS SpA (Zogno, Italy and Caledonia, Mich., U.S.) officially debuted Kreator, its hybrid composite large-format 3D printer and multi-axis milling machine. In July, the first commercial project developed with this technology was announced, in partnership with fabricator . (Varano de’ Melegari, Italy).
According to Laura Sommariva, junior communication specialist at Bercella, CMS and Bercella began working together about four years ago, with discussions about ways to innovate the composite layup process and shorten the supply chain, specifically for automotive composite parts. These conversations resulted in Bercella partnering with CMS during the development of the Kreator hybrid printer/machine center, with Bercella contributing knowledge and experience in industrial use cases.
“The goal of the partnership was that Bercella would be the industry partner who helped CMS bring their machine to market,” Sommariva says.
Hybrid LFAM/milling machine
The resulting machine is Kreator. Developed alongside Fraunhofer IWU and part of CMS’ Ares machining center line, Kreator combines large-format additive manufacturing (LFAM) with milling. The goal is to print composite components such as tooling and jigs and then immediately finish the parts within the same machining center — saving both time and the labor required to move parts from one machine to another.
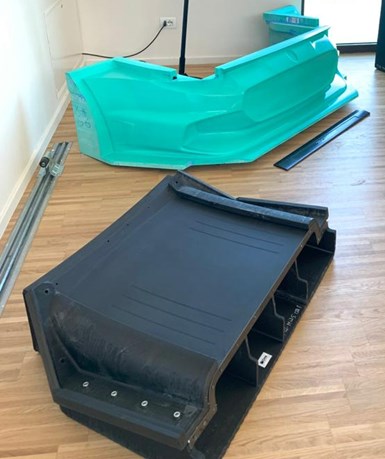
A carbon fiber composite model (black) shown beside a carbon fiber-filled polyamide mold (green) 3D printed using CMS’ new hybrid 3D printing/milling machine.
The pilot version of the machine, launched this year, is a single-screw extrusion printer compatible with 40% carbon fiber-filled polyamide 6 (PA6). Additional fiber lengths and resins, including thermoplastics, are currently being qualified, and capabilities such as larger build volume or dual heads for simultaneous printing and milling are being developed.
First use case: Carbon fiber vehicle restoration
The first project CMS and Bercella undertook is called Restomod Maserati, a challenge launched by Tomaso Trussardi to the Motor Valley for restoring his Maserati 3200 GT, for which Bercella is tasked with delivering new, reengineered carbon fiber composite body components.
For the car, called Restomod Maserati MV 3200 GTC, Bercella redesigned 26 total body components — including the door, roof, hood and front and rear bumpers — reimagining them with wider, more modern designs. Each component is built from carbon fiber prepreg, manufactured via hand layup on a 3D-printed mold, then cured via autoclave. Using a CMS Kreator machine, 20 individual molds were printed from 40% carbon fiber-filled PA6.
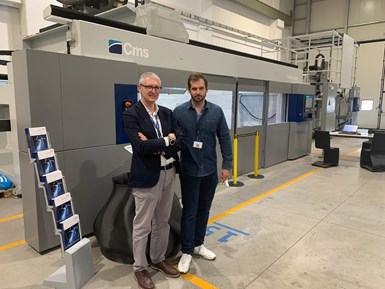
The CMS Kreator machine enables faster, zero-waste production of carbon fiber-filled molds or other components, by combining large-format additive manufacturing (LFAM) and milling in one work cell.
“This is the first car made with this technology,” says Franco Bercella, founder of Bercella S.r.l., in a press release. “It is an important moment, as we are making the ‘zero’ in the composite materials sector.” The CMS Kreator process enables zero-waste manufacturing of custom molds, Sommariva explains, and also saves time and money during production because 3D printing and milling occur within the same work cell.
A partially finished version of the vehicle was displayed at a Motor Valley event in the beginning of July, and is expected to be fully completed by the end of this year. The ultimate goal for the partnership is to use 3D-printed molds to produce an entire carbon fiber restoration vehicle.
“We are particularly proud to be part of this extraordinary project. Sustainability and production flexibility are the keywords that we shared with Franco Bercella years ago while talking about the enormous opportunities that a particular additive manufacturing solution for large formats could have brought to the composite materials sector. The Restomod project begins to make us touch these opportunities firsthand,” says Giovanni Negri, CEO of CMS SpA.
Related Content
Plant tour: Airbus, Illescas, Spain
Airbus’ Illescas facility, featuring highly automated composites processes for the A350 lower wing cover and one-piece Section 19 fuselage barrels, works toward production ramp-ups and next-generation aircraft.
Read MoreCarbon fiber composite pallet revolutionizes freight industry
LOG Point Pallet fuses advanced materials with innovative design and manufacturing to improve supply chains worldwide.
Read MoreFilament winding increases access to high-performance composite prostheses
Steptics industrializes production of CFRP prostheses, enabling hundreds of parts/day and 50% lower cost.
Read MoreAviation-specific battery system uses advanced composites to address electric, hybrid flight
BOLDair’s composite enclosure, compression structures and thermal runaway management enables high-performance electric energy storage.
Read MoreRead Next
Bercella develops carbon fiber monocoque for Hypercar model racer
Carbon fiber chassis, FIAS and RIAS will ensure the SCG 007 racer’s compliance with new power and weight regulations for its participation in the 2021 Le Mans 24 Hours race.
Read MoreCMS debuts hybrid LFAM/milling machine
The machining specialist has developed the first iteration of Kreator, a large-format, thermoplastic composite 3D printer and five-axis milling machine for tooling and jigs.
Read MoreComposites end markets: New space (2025)
Composite materials — with their unmatched strength-to-weight ratio, durability in extreme environments and design versatility — are at the heart of innovations in satellites, propulsion systems and lunar exploration vehicles, propelling the space economy toward a $1.8 trillion future.
Read More